Transforming Factory Operations: The Success Story of an MRO Industry Leader
A deep dive into the approach that helped improve and enhance this factories data hygiene from 53% to 93%.
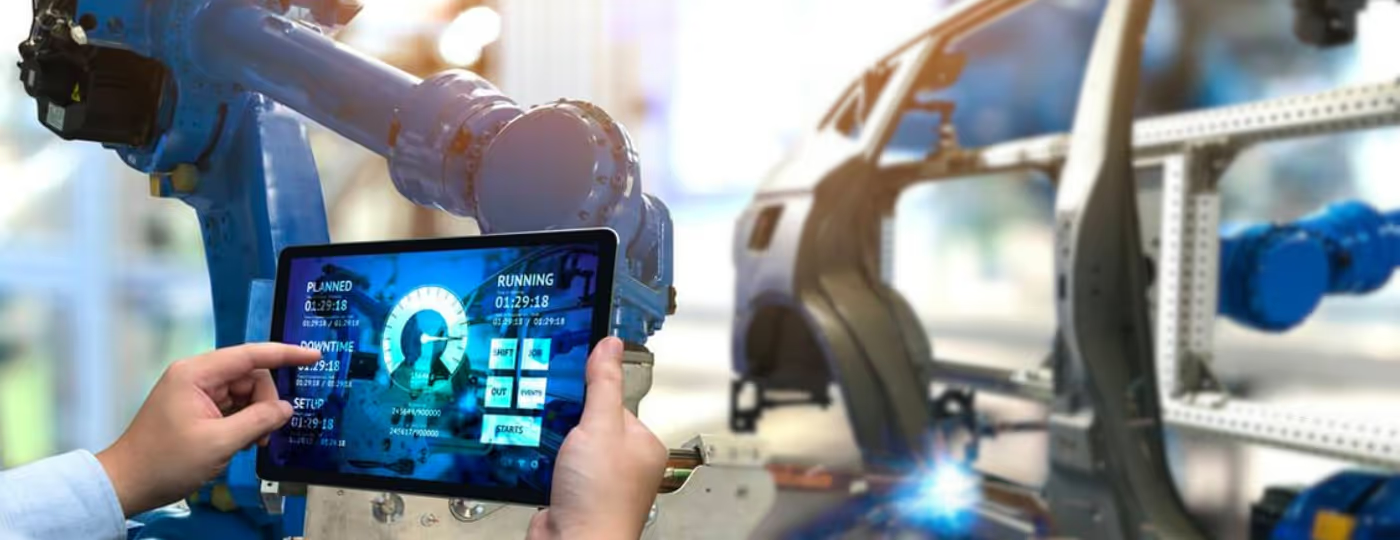
Value at Stake
Challenges
Factory Teams operating in silos with outdated data, leading to operational inefficiencies.
Inconsistent data causing frequent production and delivery delays.
Poor visibility into WIP resulting in resource misallocation.
Inaccurate data affecting production levels and impacting revenue.
Poor cross-team collaboration due to misalignment on data.
Loss of productivity to suboptimal data management endangering output volume
Objectives
Reduce WIP and improve production flow with accurate data.
Minimize data correction time to focus on higher-value tasks to increase productivity.
Ensure on-time delivery through reliable data.
Efficiently manage resources to lower operational costs.
Utilize data accuracy to increase production to maximize revenue.
Enable seamless collaboration and teamwork with unified data.
Results
In this digital transformation, a leading MRO manufacturer used Pelico’s Supply Chain Operations Platform to tackle significant data hygiene challenges. This factory was plagued by productivity loss, inaccurate decisions, collaboration issues, and revenue loss due to inaccurate data in ERP.
Within eight weeks, this factory improved its data hygiene from 53% to 93%. This substantial enhancement led to multiple operational benefits:
· Reduced Turnaround Time by 35%: By having accurate data, the factory could streamline its processes, significantly speeding up production cycles and reducing delays.
· 77% Decrease in Part Shortages: Enhanced data accuracy meant fewer instances of lost components, ensuring smoother production flows and fewer disruptions.
· 98% Reduction in Overdue Supply POs: With clean data, the factory could better track and manage purchase orders, drastically reducing the number of past-due orders and improving supplier relationships.
· 15% Increase in On-Time Delivery: Accurate data allowed for better planning and execution, resulting in more reliable delivery schedules and higher customer satisfaction.
· 18% Reduction in Work-in-Progress (WIP): Improved data quality led to more efficient use of resources, reducing excess inventory and work-in-progress items.
This improvement in data accuracy and collaboration across teams led to a significant transformation in this factory's operations, making clean data a cornerstone for daily decisions and overall performance improvement.