Will supply chain delays continue and how to respond?
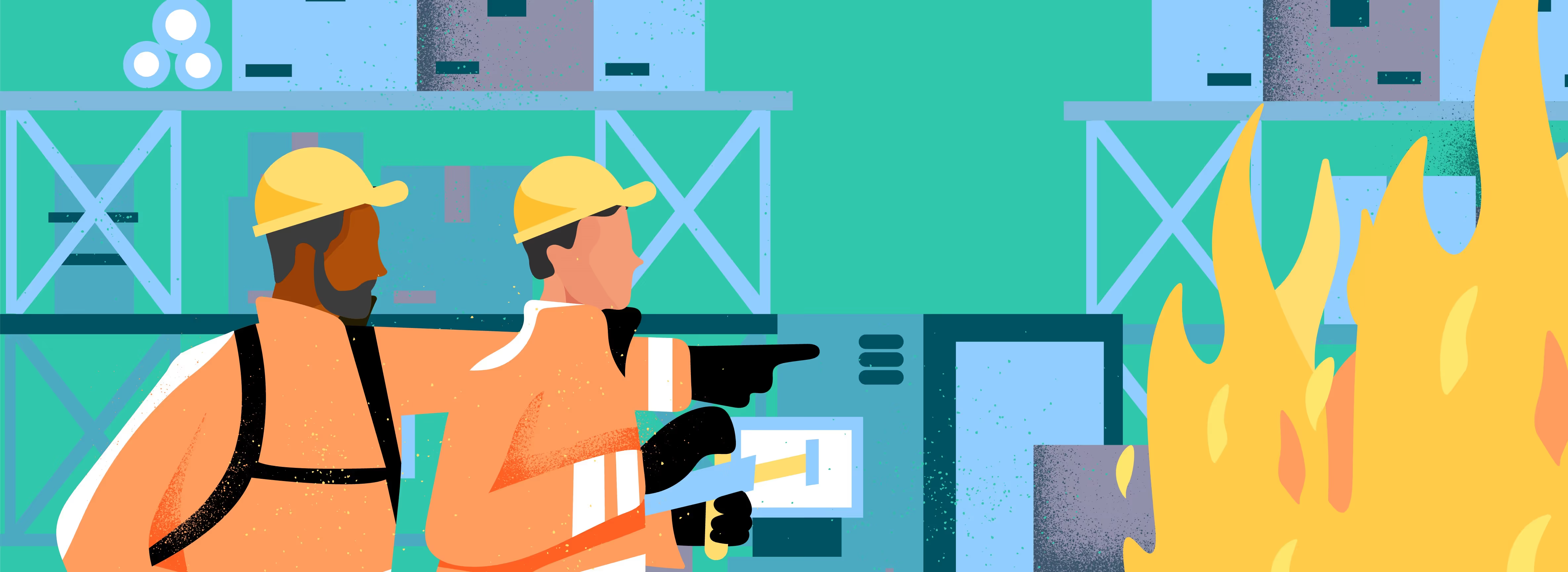
Earlier in 2022, Boeing said its 737 MAX aircraft production and deliveries were hit by shortages of a particular wiring connector. Airbus wanted to raise A320 production rates to 75 single-aisle aircraft monthly over the next three years, from 50 now. But delays in engine supplies have held back aircraft deliveries.
From multinationals to family-run stockists, few have been spared the impact of shortages or delays. "We are keeping our head above water, keeping the flow happening, but the gymnastics required to make that happen are as difficult now as they have ever been," said Stephen Timm, president of industry giant Collins Aerospace, from an interview with Reuters.
"At the moment it's extremely challenging because of the lack of raw materials," said Paul Wingfield, business development manager at Stokenchurch, England-based Aircraft Materials, which supplies alloys including aluminium, nickel, magnesium, titanium and nickel for the industry.
The global air industry is in the midst of a post-pandemic rebound, but supply chain delays and parts shortages have left suppliers and manufacturers scrambling to source everything from raw materials to small electronic components to keep production moving.
What’s the consequence of supply chain delays?
Heavy inventory and tight capital
Suppliers face lengthening lead times to source materials or components that can now run six months to over a year, threatening the manufacturers' plans to ramp up output.
To guarantee parts delivery, some suppliers are pushing manufacturers to order many months in advance, even if it means suppliers have to tie up capital by holding onto inventory for longer.
Limited possibility of switching to other suppliers
Switching suppliers can be almost impossible in a highly-regulated industry like aerospace manufacturing industry where components have to undergo rigorous approval processes.
"It's not a case of picking up and going to a different supplier, the validation process for doing that is actually often longer than the lead time," said Neil Lawrence, business development engineer at Woking, England-based Magnet Schultz. It makes solenoids - electromagnetic valves - used in everything from airplane hydraulics controls to air conditioning. Those valves range in price from a few hundred to tens of thousands of pounds. "We're getting terrible, terrible lead times on some parts," Lawrence said.
Decline in customers satisfaction
A recent research study by RSM reports that there has been a decline in customer satisfaction directly attributed to supply chain delays and parts shortages. Furthermore, over 25% of organizations they surveyed said they lost at least one important customer in the past year as a direct result. Customer churn is therefore a problem and we can foresee this only getting worse as these challenges continue.
How to respond to supply chain delays?
Improve Inventory Visibility
Knowing the status of inventory as it ships from a supplier location and being updated real-time tracking along the way will help predict possible supplier shortages and provide time to respond effectively. Deploy technology that connects all networks with one central command center. Businesses and companies can have real-time insight into their inventory from every location. Having the most accurate, up-to-date information helps leaders make key decisions when needed to pivot.
Prioritize Production
Certain products gain a higher priority when there is a material shortage or a supply chain disruption. Categorize items accordingly to keep operations flowing even if full inventory options may be temporarily limited. Also, identify capabilities, as well as potential drawbacks, of an abbreviated schedule when a supply chain disruption occurs as to not cease shipments altogether. Prioritizing the most important products first will avoid the risk of stockout. And a short-term contingency plan can keep sales steady.
Assess Alternative Logistics
Increased freight costs, port congestion, and truck driver shortages have all contributed to a significant backlog in logistics. Use advanced data analytic technology to help you identify alternative shipping options to meet changes in customer demand. Use a network optimization algorithm that pinpoints the closest warehouse to your customer base to limit costs and support on-time deliveries.
Evaluate the Market
Following any significant supply chain delays and disruptions, it’s a good idea to take stock of where the market demand is and how it may have shifted. In light of the pandemic, as an example, the increase of online ordering skyrocketed as businesses closed their physical storefronts. Now, as more people are working remotely and using technology to their shopping advantage, they want goods that meet their current needs.
Regularly reviewing data and insights from your portal will show trends in purchases and allow you to make more informed decisions about restocking or readjusting inventory.
Take Advantage of Technology
By streamlining efficiencies, new technologies will help companies lower their operational costs and be more flexible in their supply chain process. It promotes automating processes and accelerating business growth through data-driven decisions in the following aspects:
Order Management – Coordinates order fulfillment with online integration and sales channels. Users can view inventory levels, manage items, and create escalation tickets easily, all from one centralized place.
Inventory Planning – Prevents stockout or overflow emergencies through real-time inventory visibility and low stock alerts, while also forecasting trends to plan for predicted supply chain delays and disruptions and shifts in customer demand.
Network Optimization – Localizes logistics by putting products closest to where your customers are. With hundreds of fulfillment centers available throughout our distribution network, our algorithm chooses the optimal one to speed up shipping times while reducing costs.
Real-Time Visibility – Makes insights immediately available to stay ahead of potential barriers by receiving alerts and forecasting information. Tracking options help identify areas of improvement to create a more streamlined system to assist with last mile logistics.
These tools and features promote a seamless experience across the entire supply chain. Though setbacks are inevitable, how well a business is able to bounce back and move forward defines its success. Overcoming supply chain delays and disruptions is one of the biggest parts of growing and scaling a profitable business.