What is A Digital Twin and its Benefit for Manufacturing & Supply Chain?
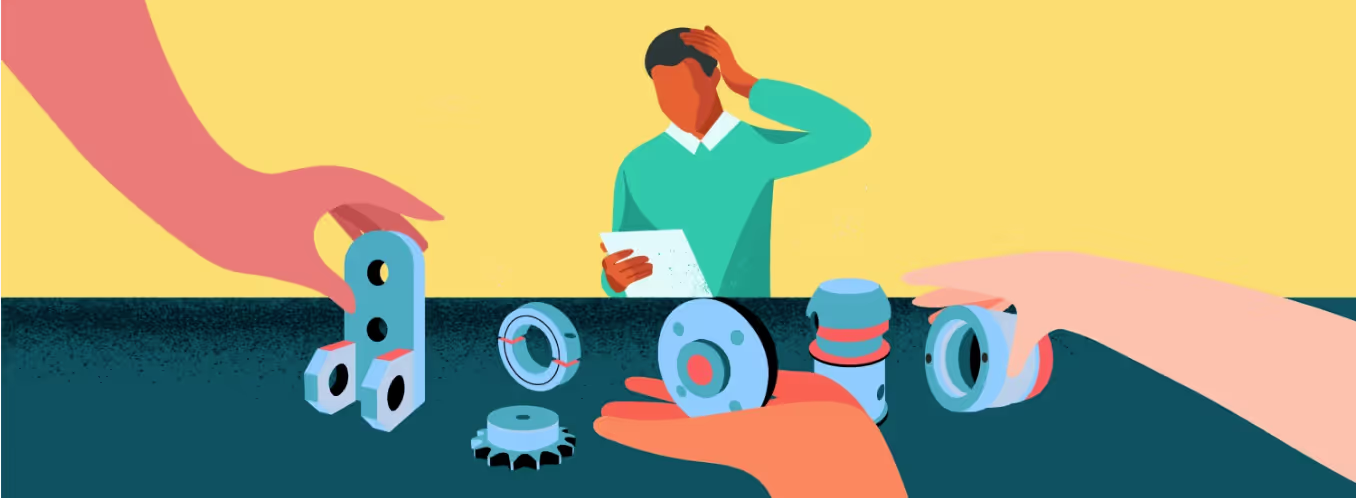
Digital twins — virtual replicas of physical entities and their interactions — consist of a combination of enabling technologies and analytics capabilities. But the technology is often misunderstood; many people incorrectly assume that digital twins are themselves sensors, 3D models, simulators, or applications of AI technology. Others mistakenly consider digital twins to be largely theoretical and not relevant for factory and supply chain management, or assume that a digital twin can be built only after the physical twin has been created — but neither statement is true.
Digital twins are a combination of multiple enabling technologies, such as sensors, cloud computing, AI and advanced analytics, simulation, visualization, and augmented and virtual reality. Companies can use a customized mix of technologies, depending on their needs and expectations. To be more specific, a digital twin in manufacturing and supply chain is a detailed simulation model which uses real-time data and snapshots to forecast factory and supply chain dynamics. From this, analysts can understand a factory’s and supply chain’s behaviour, predict abnormal situations, and work out an action plan. What distinguishes digital twins and makes them so powerful is their ability to emulate human capabilities, support critical decision-making, and even make decisions on behalf of humans.
Since the early 2000s, digital twin technology has been adopted across many industries and become more accessible and affordable, yet it remains underutilized in factory and supply chain management. This is partly explained by the complex nature of supply chains themselves and partly due to misunderstandings about the technology’s applications, capabilities, and potential value. However, with a proper adoption and implementation strategy, digital twins can deliver immense benefits across a wide range of supply chains.
Why is a digital twin needed in modern manufacturing and supply chain?
Most manufacturing and supply chain ogranizations still use static spreadsheets or planning approaches based on static assumptions to design and plan their supply chains. These tools have worked just fine in the past, but many organizations have realized that applying static models to dynamic, ever-changing real-world supply chains usually comes up short. In fact, top supply chain leaders have already embraced digital twin technology.
But a digital twin equips companies to conduct these dynamic tests and redesigns. In short, it can prove transformative. Because a digital twin enables organizations to stress test their supply chain design, it is an essential component of building a supply chain that can not only withstand setbacks, but also bounce back quickly after disruptive events like blocked transportation routes, distribution center shut-downs, and so on.
Organizations use digital twins to provide greater visibility across their supply chain, identify patterns and discover opportunities for improvement, eliminate inefficiencies, and optimize current processes. Digital twins are key enablers of supply chain resilience by helping organizations make smarter, faster, data-driven decisions to respond if and when something goes wrong.
How can a digital twin benefit manufacturing and supply chain?
By leveraging real-time data and simulation capabilities from the digital twins, numerous advantages can be achieved.
Real-time access to one source of truth
The first benefit is to have one source of truth for operations data that provides a common language for different teams working on related tasks. This means no more Excel spreadsheets with data exported manually—instead, factory and supply chain teams need real-time monitoring that’s instantly accessible, with all the contextual information necessary for decision-making. A holistic overview is essential, so links for all operations chain concepts—from purchase orders, customer orders and work orders, to quality notes, delivery events and equipment data—are needed to give teams the information they need. Since each area of factory operations impacts another area, it’s critical that this data is translated into the right information for the relevant team. No more time-wasting and extensive cognitive labor: teams need instant access to accurate, clearly presented data.
Real time monitoring of future bottlenecks with algorithmic computations
Another advantage lies in real-time monitoring of future bottlenecks through algorithmic computations enabled by the digital twins. This proactive approach allows agile and resilient factory and supply chain operations to anticipate and address potential bottlenecks. Manual calculations are insufficient, necessitating the use of algorithmic computation to consider factors such as material coverage, team and machine capacity, and various levels of granularity. By converting these bottlenecks into actionable steps, teams can focus more on problem-solving rather than searching for solutions.
Simulations of alternative plans and assessment of planning feasibility
Assessing planning feasibility is also critical for agile operations. Manufacturers need the ability to quickly evaluate the impact of alternative plans on key metrics, such as on-time delivery (OTD), coverage rate, delay, revenue, inventory levels, turn-around time, and work-in-progress (WIP). During fast-moving situations resulting from supply chain constraints, factory managers require an accurate overview of available courses of action and their potential impact. Artificial intelligence solutions play a crucial role in identifying insights and recommending optimal next actions. Additionally, digital twins offer simulation capabilities, allowing manufacturers to assess the feasibility of alternative plans through collaborative simulations.
Empowering teams to make quick decisions
In a fast-changing environment, teams need to be able to quickly identify the right decisions to take to avoid production disruptions. ****This can be achieved by enlisting the help of a powerful AI that can automatically identify the best course of action in any given situation, thereby optimizing operations planning. It should also be capable of assessing the feasibility of alternative plans (i.e. formulating digital twin scenarios) and simulate their impact on the entire factory plant operations, as well as on specific teams.
Transparent data-driven leadership
The benefits of agile factory operations extend to leaders, too. Smart technological systems will need to enable smooth communication with executives on the status of operations, meaning leaders would be able to measure the gap between the Master Production Schedule and actual factory status. They would also be able to communicate this information to relevant stakeholders, and assess different alternative operations plans—and implement the optimal one—based on their impact on the factory north star metric.
How to implement a digital twin in manufacturing and supply chain in less than 2 months
After talking about the benefits of digital twins, let’s take a look at how Pelico helps manufacturing and supply chain organizations implement a digital twin in just 2 months.
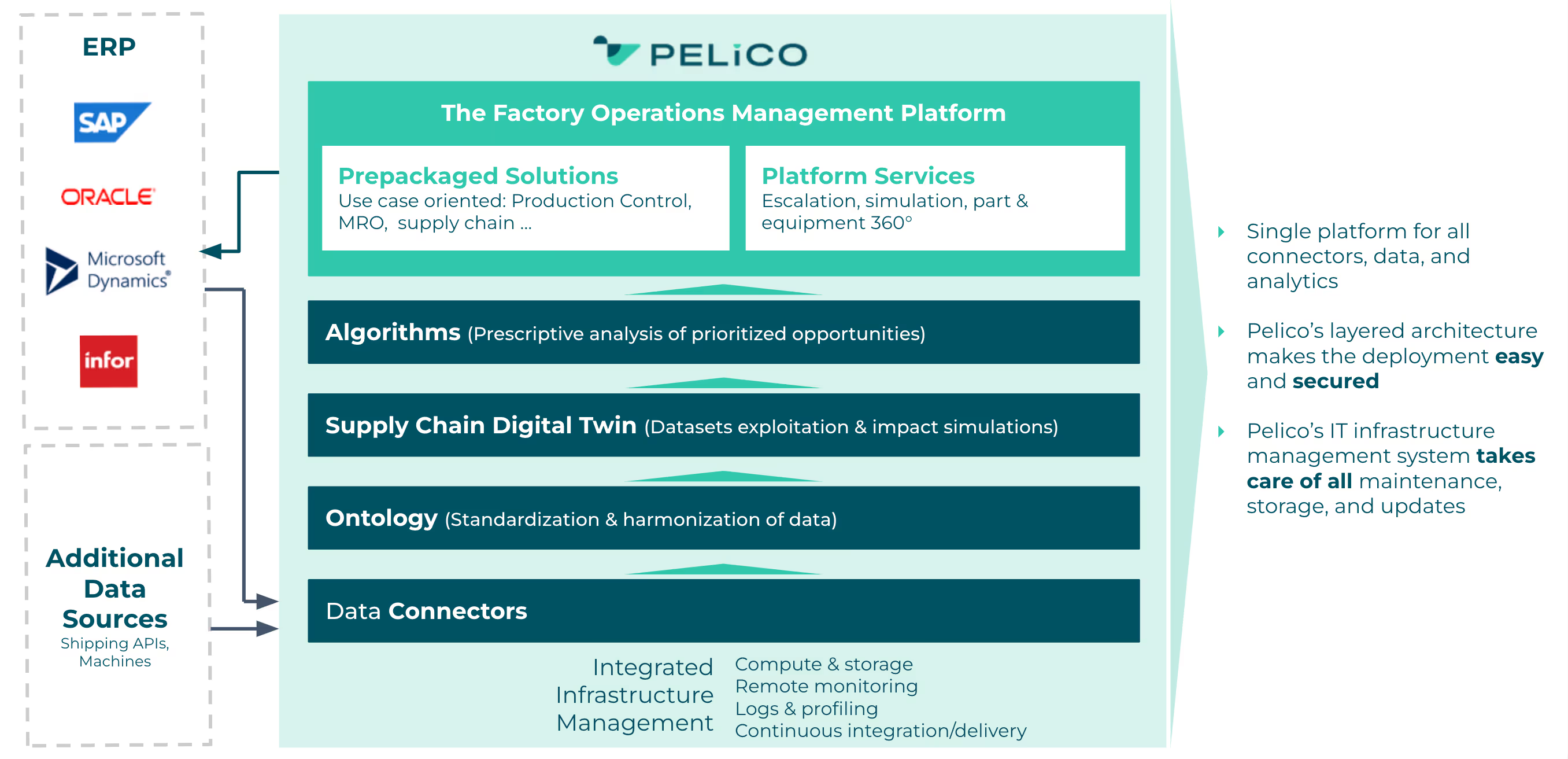
The journey begins by mapping the existing data and how it is used in existing routines. Pelico then activates the data extraction from the organization's ERP system to gather the required data to feed Pelico's platform. The frequency of data refresh can be customized by Pelico's Customer Operations team, considering preferred operational routines and organizations’ system infrastructure constraints. Concurrently, all data pipelines are continuously monitored. Pelico teams also manage the cleaning of data during this step.
Once the data foundation is established, teams can collaborate effectively on Pelico's platform. The combination of advanced algorithms and digital twins empowers factory and supply chain teams to conduct prescriptive analyses, prioritize opportunities, and simulate alternative plans.