6 examples of how AI will disrupt manufacturing operations in the near future
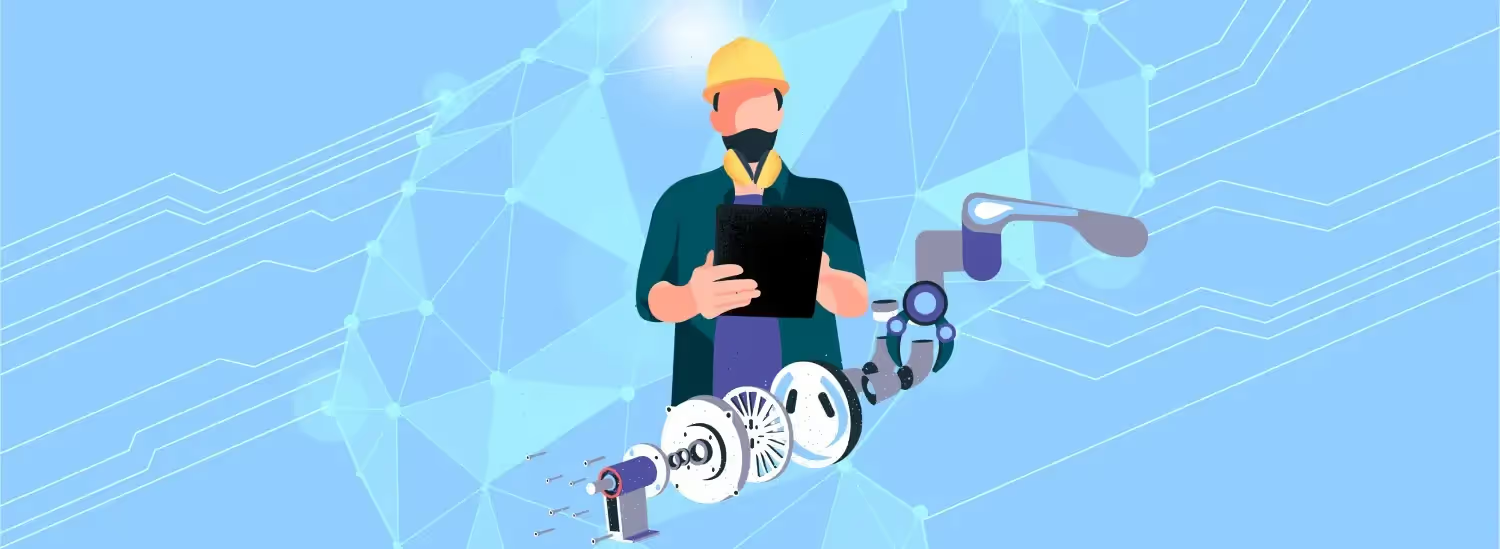
More than a year after the coronavirus pandemic forced manufacturers to halt or alter their activities and disrupted global supply chains, the idea that economic activity will resume to normal seems like a semi-distant dream. Even among those industries that have somehow managed to thrive during the pandemic—such as technology, health care or construction and remodelling, for instance—most have faced difficulties in matters such as increased raw material costs, inefficiencies in inventory management, and the challenge of attracting and retaining a quality workforce in the midst of a high-volatility environment.
Better times, however, seem to be ahead. According to a recent survey from the US National Association of Manufacturers, nearly 88% of manufacturers claim to be either somewhat or very positive about the outlook for their company. This is somewhat unsurprising given the possibilities that lie ahead with the advent of digitization, automation and, especially, artificial intelligence (AI).
Connecting the dots
The potential of these technologies is set to revolutionize manufacturing, and most are thinking ahead—according to a report by PWC, 91% of industrial companies are investing in digitizing their factories and more than half already use data to optimise their resource use.
But gathering and integrating data is only one part of the equation. Data can flow from almost every tool on the manufacturing process—be it in ERP systems, time-tracking or quality management tools or CRMs. The real challenge, however, is in connecting the dots inside the factory and analysing the patterns to inform better decisions in the manufacturing process. That is where artificial intelligence comes into place.
AI: The real game changer
Artificial intelligence can process terabytes of data emanating from sensors, machines, and people that no human could possibly analyse. By implementing machine and deep learning models and enabling automation in its operations, manufacturers can observe patterns and predict the impact of a single variable within a complex system. This gives them access to the tools to reduce costs and increase efficiency that, until now, most companies could not afford.
And while the potential of this technology is still far off—only 9% of digital factories were using artificial intelligence in 2020—there are many areas of the production process where we can already envision how the game will change forever.
- Quality inspection: visual inspections are an essential part of any production line. Quality-control or defect-assessment processes have to be performed regularly, often with several inspectors involved, which results in a costly and time-consuming procedure. Most of all, it is highly prone to human error. These errors can occur in as much as 20% to 30% of all visual inspections.
Today, image processing technology can assist or fully take over quality checks, being able to identify, with greater accuracy and speed than the human eye, defective items or missing parts. Furthermore, this technology can be deployed at a low-cost, un-intrusively and even in dangerous environments, surpassing the standard of manual inspection.
Two industries where real-time high-resolution image analysis of the assembly line can be critical are the automotive or consumer products industries. Audi, for example, has been one of the leading car manufacturers in introducing AI in its testing process during the production phase. - Preventive maintenance: maintenance of machinery and production assets represents 29% of already existing AI implementations in manufacturing—the area where most efforts are set, according to Capgemini’s Scaling AI in Manufacturing Operations: A Practitioners Perspective report.
Through the use of machine learning in computer-aided modelling, or the already mentioned visual inspections of equipment, manufacturers can move from a reactive mindset in their maintenance operations—dependent on scheduled inspections or even equipment failure— to predictive maintenance which involves tailoring maintenance routines to each piece of equipment. This new approach is a big cost-saver. According to the Robotic Industries Association, the cost of one minute of downtime in the production line for a company like General Motors can reach $20,000. That’s why GM has recently started using computer vision in its factories to identify failures in its assembly robots. In a pilot test of the system, it detected 72 instances of component failure across 7,000 robots, allowing the company to resolve the issue before it led to an outage.
- Workplace safety: The COVID pandemic has shown how reducing worker density in factories can prove critical in the midst of viral outbreaks. Some companies have already deployed computer vision algorithms that automatically monitor social distancing measures, opening up the possibility that in the near future, AI will improve not only the efficiency of factories, but also the safety of their working conditions.
- Energy management: better analysis of the operations and improved forecasting can also result in a more efficient energy use, not only reducing the overall consumption but also activating the most energy-consuming processes during off-peak periods, when electricity prices drop. The Canadian firm Novacab, for instance, has developed a hybrid energy storage system which has cut its energy consumption by 14%-40%. Furthermore, automation and robotic production are enabling energy-saving innovations such as the appearance of “dark factories”, which do not need light to function and can work 24/7.
- Supply chain management: in order to maintain a smooth-running supply chain, companies have to coordinate with suppliers and partners to avoid risk of shortage or a halt in production. Consequently, AI implementations in supply change management—which also involves logistics, inventory management, and warehousing—thus allow managers to automate the most complex and time-consuming tasks and focus on using the gained insights to more strategic and impactful decisions for the company.
- Production planning: lastly, with better and more data on the supply chain capabilities also comes better production forecasting. AI helps predict outputs of production, such as lead times, yields based on historical performances, and current conditions. It also helps anticipate blockers and recommend mitigation scenarios such as reallocating resources or rescheduling to maximize throughput and minimize costs. This means AI enables one to react more efficiently to daily volatility.